Why HDPE
HIGH-DENSITY POLYETHYLENE Pipes
WHY HDPE
Damage Resistance: HDPE has low notch sensitivity, providing a high level of resistance to the effects of external damage, especially important for pipe bursting operations and others where there is likelihood of such damage.
Abrasion Resistance: HDPE pipes have excellent abrasion resistance providing long life in abrasive slurry applications. In most of these applications HDPE pipe outlasts other pipe materials such as mild steel and rubber lined steel.
Chemical Resistance: Outstanding resistance to a wide range of chemical reagents allows the use of polyethylene systems in applications such as: Tailings pipelines and chemical treatment applications.
Flexibility: HDPE pipes are flexible and can be bent to a minimum bending radius of 30 times the pipes outside diameter. This flexibility is critical in applications such as mine subsidence and earthquake prone areas. This inherent resiliency and flexibility allows the pipe to absorb surge pressures, vibration and stresses caused by soil movement.
Ease of Installation: HDPE pipes are easy to install with their light weight and long lengths. Polyethylene coiled pipes are widely used in applications such as stock watering, irrigation systems, communication, gas and reticulated water mains due to rapid installation and the ease and less frequent jointing.
High Flow Capacity: HDPE pipes have lower friction factors than most non-plastics materials. The surface energy characteristics of HDPE ensure that material deposition is inhibited and the smooth bore characteristic is maintained over the working life of the pipeline.
Long Life: HDPE pipes have a proven high reliability record across a wide range of industries and applications, now approaching a period of 50 years. HDPE also provides a long maintenance free lifetime with low whole life costs, compared to many other materials.
-
EN ISO 9001:2015 Standard
-
ISO 9001:2014
-
ISO 45001:2018
-
Fully satisfaction guarantee


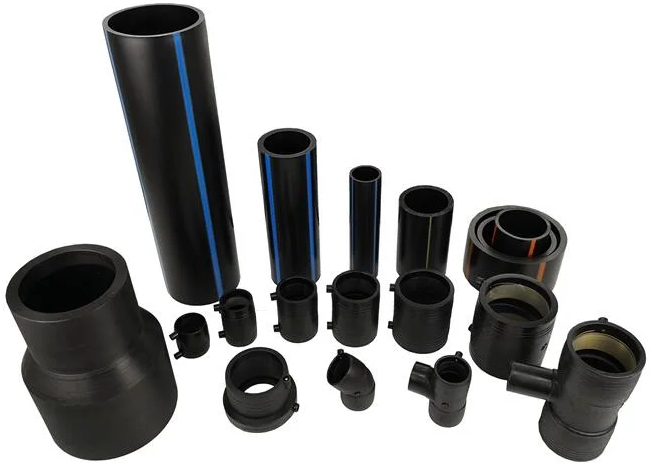